Chromium is a hard metal that is resistant to corrosion. It is widely used in metallurgy, chemical, cast iron, fire-resistant, and high-end technology. The specific application ratio is shown in the following figure:
Chromium in the Metallurgical Industry
Chromium is a hard metal, and is often incorporated into steel to make hard and corrosion-resistant alloys. Those alloys are mainly used to refine stainless steel, heat-resistant steel and various electric heating materials. When stainless steel encounters corrosive substances, its surface will form a fine and solid chrome oxide film, which protects the internal metal from corrosion. Some stainless steel can maintain its excellent performance even at high temperature of 800 °C. Chrome steel is a good material for manufacturing machinery, tanks and armored vehicles.
Chromium in the Chemical Industry
Chromium salt is one of the main varieties of inorganic salts and is the main raw material in the chemical industry. It is widely used in daily life, including electroplating, tanning, printing and dyeing, medicine, fuel, catalyst, oxidant, match and metal corrosion inhibitor.
At the same time, metallic chromium has been listed as one of the most important coating metals–chromium sputtering targets for sputter deposition and chromium evaporation materials for evaporation coating. In most cases, the chrome layer is specifically used as the outermost coating for the parts. When chrome is applied, the thinner the chrome layer, the closer it is to the surface of the metal. The chrome layer on the inner walls of some is only five thousandths of a millimeter thick, but after firing thousands of rounds and bullets, the chrome layer still exists. If the surface is not chrome-plated, the service life of most parts will be greatly shortened due to wear and corrosion, and must be replaced or repaired frequently. Therefore, chrome plating is widely used in many industrial manufacturing.
Chromium for Refractory and Cast Iron
Chromite has a high melting point of 1900 °C – 2050 °C, and it can maintain the volume at high temperature and does not react with any slag, so it is used as a lining for refractory materials, steelmaking furnaces and non-ferrous metal smelting furnaces.
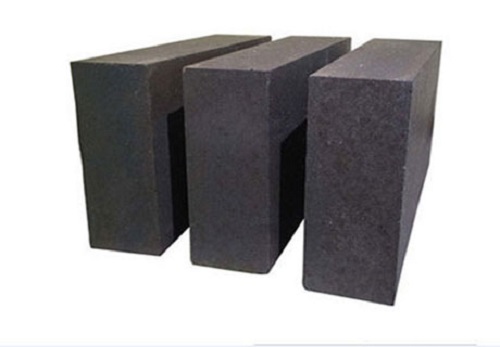
Chromite can be used to make chrome bricks, chrome-magnesia bricks and other special refractory materials. In addition, chromium is also used in cast iron, such as chromium cast ductile iron, which has high strength, high elongation, high impact value and low hardness.
For more information, please visit https://www.sputtertargets.net/.