Introduction to Pulsed Laser Deposition (PLD)
In the world of materials science, the quest for precision and versatility in thin film preparation has led to the development of several advanced techniques, among which Pulsed Laser Deposition (PLD) stands out.
PLD, also known as Pulsed Laser Ablation, harnesses the power of a laser to bombard the surface of a target material. This process elevates the surface temperature significantly, producing high-temperature and high-pressure plasma (T > 104K). The material then deposits on various substrates to form a thin film. This technique is celebrated for its ability to create films with unparalleled precision, catering to a wide range of applications from microelectronics to optical technologies.
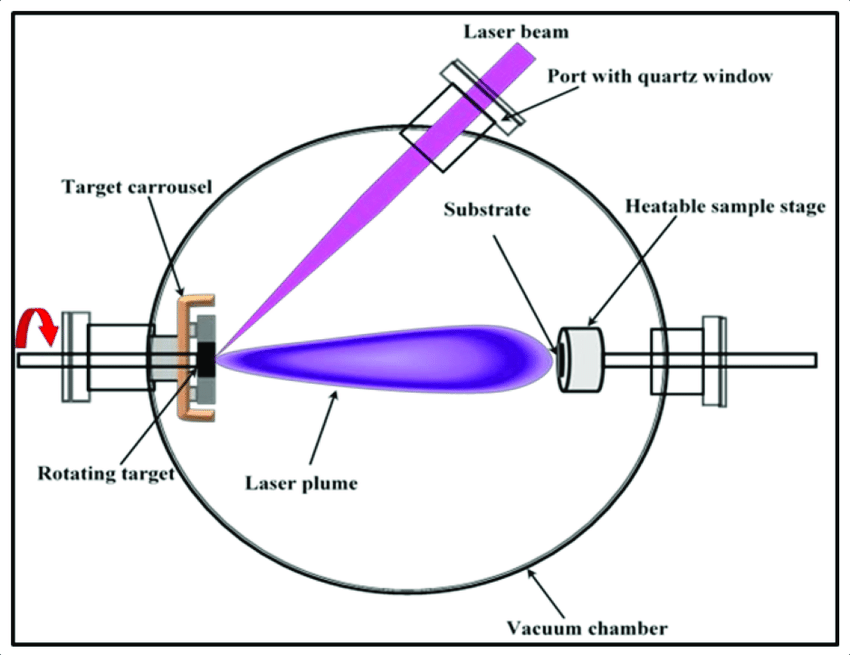
Advantages of PLD
Multi-component Films
One of the hallmark advantages of PLD is its adeptness at producing multi-component films that maintain the desired stoichiometric ratios with ease. This characteristic is particularly beneficial in applications requiring precise chemical compositions, making PLD a preferred method for developing advanced functional materials.
High Deposition Rate and Flexibility
PLD boasts a high deposition rate, ensuring a swift test period and minimal substrate temperature requirements. This efficiency, coupled with the uniformity of the films prepared, positions PLD as a highly effective method for thin film deposition. Moreover, the process’s inherent simplicity and flexibility signal its vast development potential and compatibility across a broad spectrum of materials science endeavors.
Adjustable Process Parameters
The ability to arbitrarily adjust process parameters is another feather in PLD’s cap. This flexibility allows for the easy preparation of multilayer films and heterojunctions, with no limitation on the type of PLD targets. The adaptability in choosing multi-target components further underscores PLD’s versatility in meeting diverse material preparation needs.
Non-polluting and Easy Control
Utilizing UV pulsed lasers as the energy source for plasma generation, PLD stands out as a non-polluting technique. This aspect, combined with the method’s ease of control, ensures that PLD aligns with the growing demand for environmentally friendly and easily manageable manufacturing processes in the production of thin film materials.
Disadvantages of PLD
Despite its numerous advantages, PLD is not without its challenges. One notable issue is the presence of molten small particles or target fragments in the deposited film, which can significantly compromise the quality of the film. These particles, sputtered during the laser-induced explosion, introduce defects that detract from the film’s integrity.
The feasibility of PLD for large-area deposition also remains unproven, limiting its application in industries requiring expansive film coverage. Coupled with an average deposition rate that is slow relative to other methods, these limitations suggest areas where PLD may benefit from further refinement and innovation.
Moreover, considering the cost and scale of laser film preparation equipment, PLD’s current applicability appears confined to high-tech fields such as microelectronics, sensor technology, optical technology, and new material films. This niche positioning highlights the need for continued development to expand PLD’s utility across a broader range of applications.
Stanford Advanced Materials (SAM) and PLD
In the landscape of thin film preparation, the role of reliable materials suppliers cannot be overstated. Stanford Advanced Materials (SAM) Corporation emerges as a global leader in providing a diverse array of sputtering targets, including metals, alloys, oxides, and ceramic materials. These materials are pivotal for PLD and other thin film deposition techniques, underscoring SAM’s contribution to advancing the frontiers of materials science and engineering.
Conclusion
Pulsed Laser Deposition (PLD) presents a compelling technique in the preparation of thin films, offering a unique blend of precision, versatility, and environmental friendliness. While its advantages pave the way for innovative applications, the method’s limitations highlight areas ripe for research and development. As the field continues to evolve, partnerships with materials suppliers like Stanford Advanced Materials (SAM) will be crucial in harnessing PLD’s full potential, driving forward the technological advancements that rely on high-quality thin films.