Aluminum sputter targets may seem like humble components, but their journey from high-purity aluminum ingots to precision-engineered pieces involves a fascinating process known as deformation treatment. In this article, we’ll explore the intricacies of how high-purity aluminum undergoes deformation to transform into sputter targets, contributing to advancements in thin film technology.
Introduction
Aluminum sputter targets are the unsung heroes of thin film technology, and the meticulous process they undergo is crucial to their performance. The deformation treatment of aluminum, involving forging, rolling, and heating, is the key to shaping this metal into precision targets. Let’s delve into the journey of how simple aluminum evolves through a series of controlled processes to become an essential component in vacuum coating machines.
Further Reading: An Overview of Aluminum Sputter Target
High-Purity Aluminum Ingot
The journey begins with a high-purity aluminum ingot—a material of utmost importance. High purity is not just a requirement; it’s a necessity. This initial stage sets the foundation for the entire process, ensuring that the aluminum is free from impurities that could compromise the quality of the resulting sputter target.
Forging: Shaping the Futur
The first significant step in the deformation treatment is forging. In simpler terms, forging involves shaping the aluminum through the application of localized compressive forces. Think of it as molding clay but on a microscopic level. The goal is to give the aluminum a preliminary form, setting the stage for subsequent processing.
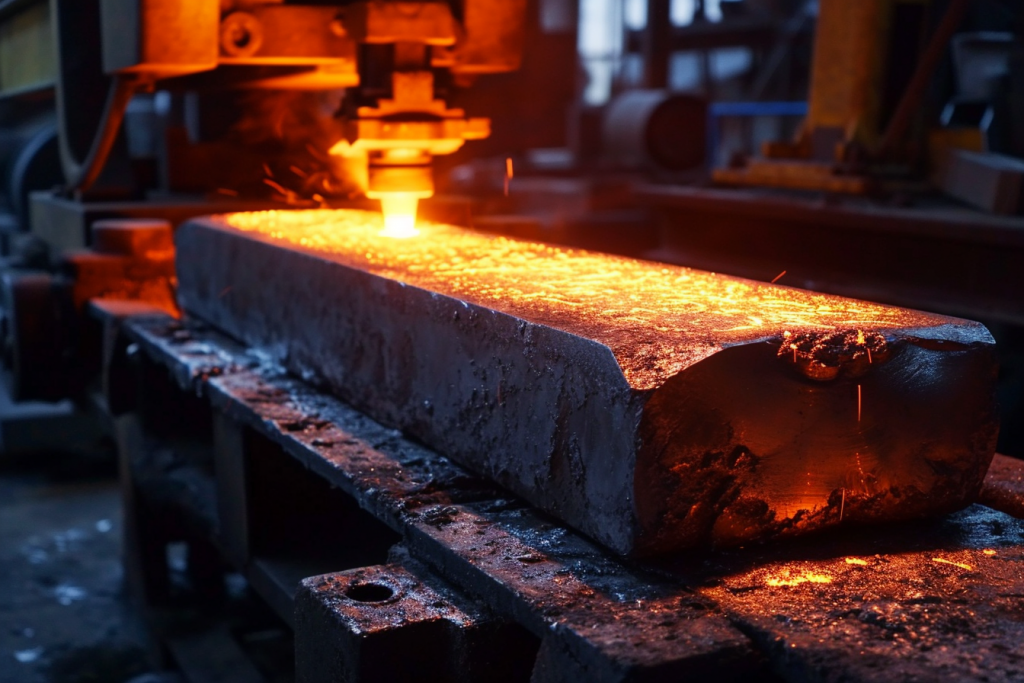
Rolling: Refining the Crystal Structure
Following forging, the aluminum undergoes rolling—a process where it is passed through rollers. This isn’t just about flattening the material; it’s about refining the crystal structure. The grains in the aluminum align, creating a more uniform and controlled structure. This refinement is crucial for achieving the desired mechanical properties.
Heating: The Controlled Transformation
Heating is a crucial stage in the deformation treatment process. Controlled heating serves multiple purposes, acting as a catalyst for stress relief, recrystallization, and the elimination of any lingering imperfections. Picture it as a controlled transformation, where the aluminum undergoes changes that enhance its overall properties.
Crystal Grain Refinement and Density Enhancement
Throughout the deformation treatment, the focus is on crystal grain refinement. Finer crystal grains contribute to enhanced strength, improved conductivity, and a more uniform material. Additionally, the density of the aluminum increases, a vital aspect for ensuring the sputter target’s performance during the thin film deposition process.
Processing into Target Size
Once the deformation treatment is complete, the high-purity aluminum material is meticulously processed into the specific size and shape required for the vacuum coater. Precision machining takes center stage, ensuring that the resulting sputter target meets exact specifications, a critical factor for optimal performance.
High Precision and Surface Quality
Precision is paramount in the final stages of the deformation treatment. The processed aluminum must meet stringent standards for both high precision and surface quality. Any imperfection on the surface could compromise the performance of the sputter target, emphasizing the importance of attention to detail in this intricate process.
Conclusion
In conclusion, the deformation treatment of aluminum sputter targets is a journey that transforms a seemingly ordinary material into a crucial component of thin film technology. From the high-purity aluminum ingot to the meticulously processed sputter target, each step plays a vital role in ensuring optimal performance in vacuum coating applications.
Understanding the deformation treatment journey sheds light on the complexity behind the seemingly simple sputter targets, highlighting the precision, care, and engineering prowess required to contribute to advancements in thin film technology.
By appreciating this journey, we gain insight into how a basic metal can undergo controlled transformations, evolving into a component that drives innovation in various industries. The deformation treatment of aluminum sputter targets is a testament to the intersection of simplicity and sophistication in the world of materials science.
For more information, please visit SAM Sputter Targets.