The most popular surface treatment technologies, chemical vapor deposition (CVD) and physical vapor deposition (PVD), have been used extensively for nearly 50 years to harden the surfaces of tools and molds. The context that follows compares the technologies and processes of CVD and PVD using the illustration of cutting tools.
Rationale
In the process known as chemical vapor deposition (CVD), a vapor containing a gaseous reactant or a liquid reactant that makes up a thin film element as well as other gases necessary for the reaction are introduced into a reaction chamber in order to chemically react on the surface of the substrate to form a thin film.
Physical vapor deposition (PVD) uses low-voltage, high-current arc discharge technology under vacuum conditions to evaporate the target and ionize the vaporized material and the gas, and finally make the evaporated material and its reaction deposited on the workpiece.
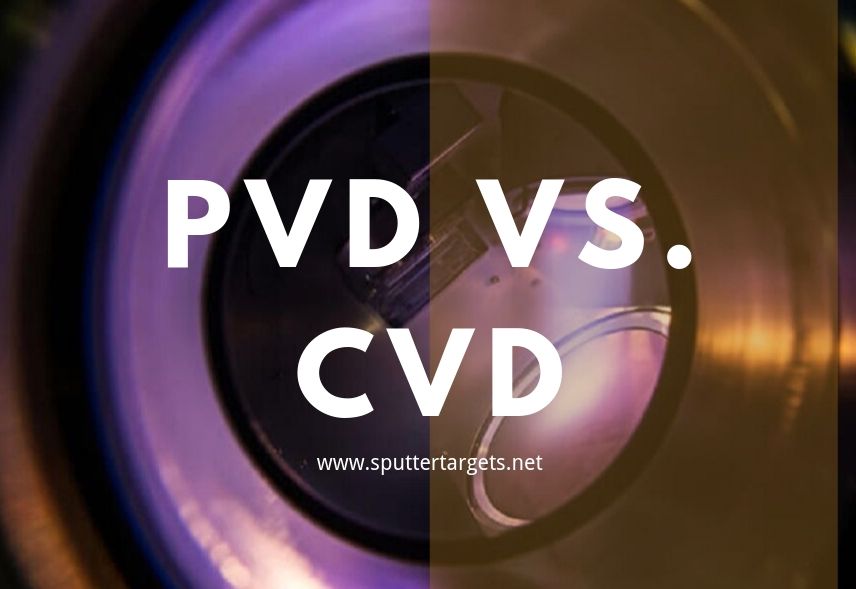
Process and Equipment
1. Temperature
The fundamental distinction between CVD and PVD is temperature. The tools must undergo a vacuum heat treatment after coating since the process temperature of the CVD method is higher than the high-speed steel’s tempering temperature. This will restore the tools’ hardness.
2. Compared to PVD, the CVD method requires less cleaning of the tool entering the reactor.
3. The PVD coating (approximately 2.5 m) is thinner than the CVD coating (about 7.5 m) on the tool’s surface.
4. The CVD coating’s surface is marginally rougher than the substrate’s surface. On the other hand, the PVD coating has a good metallic sheen without grinding and effectively reflects the tool’s surface.
5. The crafting process
CVD has good coating performance and takes place in a gaseous atmosphere with low vacuum. Hence, every surface of the cutters encased in the reactor, including deep holes and inner walls, can be entirely coated, with the exception of the support points.
In contrast, all PVD technologies have poor coating performance both on the back and sides of the tool due to low air pressure. To prevent the production of shadows, the PVD reactor must minimize its loading density, and loading and fixing are challenging. In a PVD reactor, the tool typically revolves constantly, though occasionally it must also reciprocate.
6. Cost
Although the PVD production cycle is one-tenth that of CVD, the initial equipment expenditure is three to four times that of CVD. Whereas PVD is severely constrained, a wide range of workpieces can be treated within a CVD operating cycle. In other words, PVD can cost more than CVD in some cases.
7. Safety
As a form of “green engineering,” PVD creates less pollution when operating. Contrarily, the reactive gas and reaction tail gas of CVD may have some corrosiveness, flammability, and toxicity, and the reaction tail gas may contain powdered and fragmented chemicals, thus particular precautions for the equipment, environment, and operators must be taken.
Stanford Advanced Materials supplies high-quality and consistent products to meet our customers’ R&D and production needs. You can visit our website for more information.
dear Author –
many thanks — your article was extremly helpful to us…
explicit interesting and very well writen and presented —
we will continue to refer to your web site for the varios coating method clarifiations.
keep it up we are waiting –