The evaporation source is a heating element used to vaporize the molding material. The evaporation sources currently used mainly include the following types:
Resistance evaporation heating source
The resistance heating method is simple and easy to operate, and is a common application method: a filament-like or sheet-like high melting point metal (such as Tungsten, Molybdenum, Titanium, etc.) is made into an evaporation source of a suitable shape. It is equipped with an evaporation material to turn on the power supply, and the evaporation material is directly heated and evaporated. The resistance heating method should mainly consider two problems, the melting point and vapor pressure of the evaporation material; the reaction of the evaporation material with the coating material and the wettability caused by the coating material.
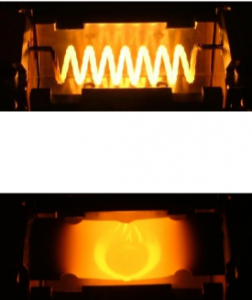
Electron beam evaporation source
The evaporation material is placed in a water-cooled copper dry pot and directly heated by an electron beam, which is called electron beam heating. It can vaporize the evaporation material and form a film on the surface of the substrate. It is an important heating method and development direction in the vacuum evaporation coating technology. In the resistance heating method, the coating material and the evaporation material are in direct contact, and the temperature of the evaporation material is higher than that of the coating material, and is easily mixed into the coating material, especially in the semiconductor device coating. Electron beam evaporation can overcome many shortcomings of general resistance heating evaporation, and is particularly suitable for preparing high melting point film materials and high purity film materials.
High frequency induction heating evaporation source
The high-frequency induction heating evaporation source places the graphite or quartz crucible containing the evaporation material in the center of the water-cooled high-frequency spiral coil, so that the evaporation material generates strong eddy current loss and hysteresis loss under the induction of the magnetic field in the high frequency band (to Ferromagnetic), causing the evaporating material to heat up until evaporation. The smaller the volume of the evaporated material is, the higher the frequency of induction is. In the large-scale vacuum aluminum plating equipment on the steel strip, the high-frequency induction heating evaporation process has achieved great success.
Radiant heating evaporation source
For materials with high absorption of infrared radiation, it can be evaporated by radiant heating, and many substances are evaporated by this method. In addition, the reflectivity of the metal for infrared radiation is high, and the absorption rate of quartz for infrared radiation is low, so they are difficult to be evaporated by radiation heating. The main advantage of the radiant heating method is that the evaporation is only heated on the surface, and the adsorbed gas is released on the surface without splashing the material.
Laser beam evaporation source
The evaporation technique using a laser beam evaporation source is an ideal film preparation method because the laser can be installed outside the vacuum chamber. This not only simplifies the space arrangement inside the vacuum chamber and reduces the abandonment of the heating source, but also completely avoids the contamination of the evaporation material by the evaporator, thus it is advantageous for obtaining a high-purity film.
Stanford Advanced Materials (SAM) Corporation is a global supplier of various sputtering targets such as metals, alloys, oxides, ceramic materials. If you are interested, please visit our website https://www.sputtertargets.net/ for more information.