Introduction
In the cutting-edge realm of aerospace electronics, selecting the optimal materials for component manufacturing is not just a matter of efficiency; it’s a vital necessity. Aerospace components must withstand an array of extreme conditions, from the searing heat of re-entry to the biting cold of outer space, all while maintaining impeccable performance. Central to the process of creating these resilient components is the evaporation of metals, a technique pivotal in depositing thin films of conductive materials onto electronic components.
Here, the choice of crucible material—specifically, when using aluminum (Al) evaporation materials for its notable conductive properties—becomes a critical decision. Boron nitride (BN) crucibles emerge as a superior choice due to their remarkable thermal stability and low reactivity. This synergy between aluminum and BN crucibles underscores a significant advancement in the manufacturing of aerospace electronics, promising enhanced thermal and electrical performance under the most challenging conditions. This article delves into the crucial role of materials selection in aerospace applications, focusing on the unparalleled benefits of aluminum evaporated in boron nitride crucibles.
Read more: Crucible Selection for Evaporation Materials: A Comprehensive Guide
Overview of Aerospace Electronics Challenges
Aerospace electronics are subject to some of the most demanding environmental conditions imaginable. These components must perform reliably at extreme temperatures, ranging from the intense heat experienced during high-speed atmospheric re-entry to the sub-zero cold of outer space. Moreover, they are exposed to vacuum conditions where traditional cooling methods are ineffective, and they must resist radiation that can degrade electronic performance over time.
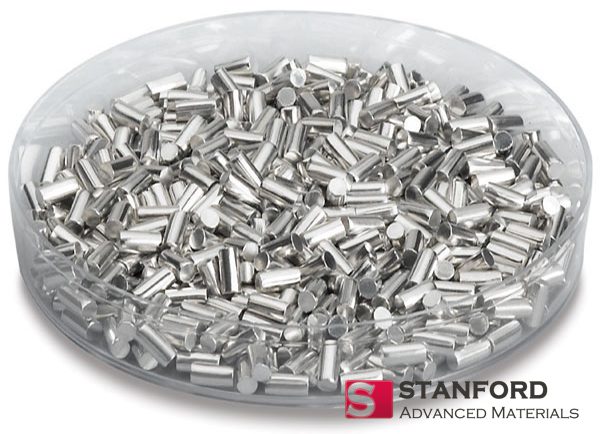
Extreme Temperatures and Thermal Management: The vast temperature variances in aerospace environments pose a significant challenge. Electronics need to maintain functionality and integrity whether they’re exposed to intense heat or extreme cold. This requires materials that can ensure thermal stability across a broad temperature spectrum.
Vacuum Conditions: The vacuum of space presents unique challenges for thermal management. Without air for convective cooling, materials must efficiently dissipate heat through radiation or conduction to other surfaces, a task that demands materials with excellent thermal conductivity and stability.
Radiation Resistance: Cosmic and solar radiation in space can induce lattice defects in semiconductor materials, leading to performance degradation over time. Aerospace electronics require materials that can withstand or mitigate the effects of this radiation, maintaining their functional integrity throughout the duration of their mission.
Given these challenges, the selection of materials for aerospace electronics goes beyond simple functionality. It requires a comprehensive understanding of the environment in which these components will operate. Aluminum, known for its excellent thermal and electrical properties, emerges as a key player in this domain. However, the success of aluminum in aerospace applications is significantly enhanced by the use of boron nitride (BN) crucibles in the evaporation process, a method that ensures the purity and performance of aluminum coatings.
Aluminum in Aerospace Applications
Aluminum stands out in aerospace applications for several reasons. Its high electrical conductivity makes it ideal for electronic components, ensuring efficient signal transmission. Furthermore, aluminum’s low density contributes to the overall reduction of component weight, a critical consideration in aerospace engineering where every gram counts.
Thermal Properties: Aluminum’s ability to conduct heat effectively allows for the efficient dissipation of thermal energy, an essential trait for components exposed to the extreme thermal variations of aerospace environments. This property is particularly beneficial in managing the thermal loads on electronic systems during missions.
Corrosion Resistance: Aluminum naturally forms a protective oxide layer when exposed to the atmosphere, offering resistance against corrosion. This characteristic is vital for the longevity and reliability of aerospace components, which must endure long durations in challenging environments without succumbing to degradation.
Reflectivity and Shielding: The reflective properties of aluminum coatings can also serve to protect spacecraft and satellites from solar radiation, acting as a thermal shield. Additionally, aluminum can provide electromagnetic shielding for sensitive components, protecting them from harmful interference.
The Role of Boron Nitride (BN) Crucibles
The pivotal role of BN crucibles in the evaporation of aluminum for aerospace applications cannot be overstated. Boron nitride, with its exceptional properties, complements aluminum’s characteristics, ensuring that the evaporation process enhances the aluminum’s inherent advantages.
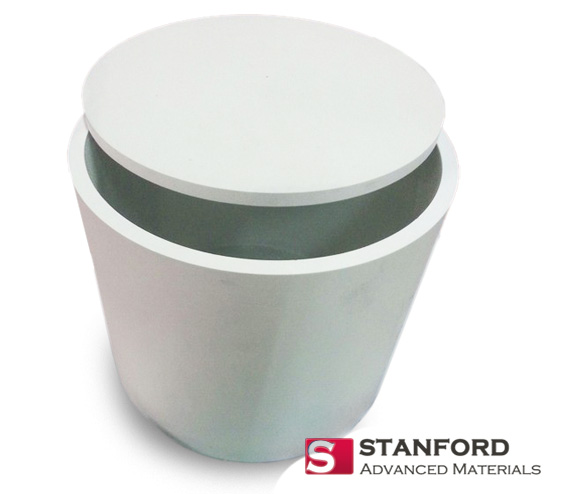
Thermal Stability: BN crucibles offer unparalleled thermal stability, a necessary attribute for processes involving high temperatures. This stability ensures that the crucible does not degrade or react with the aluminum during evaporation, maintaining the purity of the deposited film.
Low Reactivity: The chemical inertness of boron nitride is another critical factor. Its low reactivity with aluminum at evaporation temperatures prevents contamination of the metal, ensuring that the resultant thin films are of the highest quality. This is paramount in aerospace applications where even minor impurities can significantly impact the performance and reliability of electronic components.
Non-Wetting Surface: BN crucibles possess a non-wetting surface, which prevents the adherence of aluminum to the crucible walls during the evaporation process. This feature simplifies the process of evaporation, allowing for more efficient and uniform coating of aluminum on the target components. It also facilitates easier cleaning and maintenance of the crucibles, enhancing their lifespan and reducing operational costs.
Advantages of Using Aluminum with BN Crucibles
The pairing of aluminum with boron nitride (BN) crucibles in the evaporation process brings forth a synergy that significantly benefits aerospace electronics manufacturing. This combination leverages the unique properties of both materials to enhance the thermal and electrical performance of aerospace components under extreme conditions.
Enhanced Purity and Performance: The non-reactive nature of BN crucibles with aluminum ensures that the evaporated aluminum remains highly pure. This purity is paramount in aerospace applications, where even minor impurities can drastically affect the electrical conductivity and thermal properties of components. The high-quality aluminum layers produced contribute to the improved efficiency and reliability of electronic systems, essential for applications ranging from communication satellites to spacecraft.
Uniform Coating Distribution: BN crucibles facilitate a consistent and uniform distribution of aluminum during the evaporation process. This uniformity is crucial for achieving even coatings on electronic components, which in turn, ensures consistent performance across the entire system. Uniform coatings help in minimizing hot spots and improving the overall thermal management of aerospace electronics, a critical aspect in the longevity and reliability of these components.
Thermal Stability Under Extreme Conditions: The excellent thermal stability of BN crucibles means that they can withstand the high temperatures required for aluminum evaporation without degradation. This stability ensures that the evaporation process can be tightly controlled and repeated with high precision, a necessity for producing aerospace components where consistency and reliability are non-negotiable.
Operational Efficiency: The use of BN crucibles in aluminum evaporation for aerospace electronics not only improves the quality of the components produced but also enhances the operational efficiency of the manufacturing process. The durability and longevity of BN crucibles reduce the need for frequent replacements, lowering downtime and maintenance costs.
By leveraging the advantages of aluminum and BN crucibles, aerospace electronics manufacturers can achieve superior component performance, enhanced reliability, and operational efficiency. This strategic material selection plays a pivotal role in advancing aerospace technology, meeting the industry’s stringent requirements, and pushing the boundaries of what is possible in extreme environments.
Case Study: Application in Aerospace Electronics
Material: Aluminum (Al)
Crucible: Boron Nitride (BN)
Scenario: Enhancing Thermal and Electrical Performance in Aerospace Components
Background:
In the competitive and rigorous realm of aerospace technology, the performance and reliability of electronic components are paramount. An aerospace manufacturer faced challenges in improving the thermal management and electrical conductivity of their satellite communication systems, crucial for ensuring uninterrupted operation in the harsh conditions of space.
Solution:
The manufacturer opted for aluminum as the primary material for its excellent electrical conductivity and thermal dissipation properties. To deposit aluminum onto electronic components with high precision and purity, boron nitride (BN) crucibles were selected for the material evaporation process. The choice was driven by BN’s remarkable thermal stability and low reactivity, ensuring that the aluminum layers were deposited uniformly and without contamination.
Outcome:
The use of BN crucibles for aluminum evaporation led to a significant enhancement in the thermal and electrical performance of the satellite communication systems. The components exhibited improved heat dissipation, reducing the risk of overheating and ensuring stable operation even under the fluctuating temperatures of space. Additionally, the superior electrical conductivity of the aluminum layers contributed to more efficient signal transmission, enhancing the reliability of communications.
Impact:
This strategic approach not only solved the immediate challenges faced by the aerospace manufacturer but also set a new standard for the industry. The successful application of aluminum evaporated in BN crucibles demonstrated the potential for other aerospace applications, paving the way for more advanced electronic systems capable of enduring the extreme conditions of space exploration and satellite operations.
Considerations for Material and Crucible Selection
When selecting evaporation materials and crucibles for aerospace applications, several key considerations extend beyond thermal stability and chemical reactivity. Compatibility between the crucible and evaporation material is crucial to prevent contamination and ensure the integrity of the deposited layer. Cost also plays a significant role, as the choice of materials affects not only the initial investment but also the longevity and maintenance requirements of the manufacturing process. Lastly, application-specific requirements, such as desired electrical conductivity, thermal properties, and resistance to environmental factors, must guide the selection process. Balancing these considerations ensures the successful application of evaporation materials in aerospace electronics, contributing to the advancement of durable and high-performing components.
Conclusion
The strategic pairing of aluminum with boron nitride (BN) crucibles in aerospace electronics underscores the necessity of precise material selection to satisfy the aerospace sector’s rigorous demands. This synergy not only boosts component efficacy and dependability but also highlights the role of specialized suppliers like Stanford Advanced Materials (SAM) in driving technological progress. Offering both high-quality evaporation materials and e-beam crucibles, SAM, with its expert engineers, assists in navigating these crucial choices, facilitating advancements in aerospace technologies and ensuring the success of critical missions.