Cerium is the most abundant rare earth elements. It is a silvery gray active metal, whose powder is easily oxidized in the air and soluble in acid. Cerium has been widely used in the automotive industry as a catalyst to reduce emission, and in glass industry as glass polishing materials. Cerium sputtering target is an important material in optical coating.
Discovery History
In 1803, when the German chemist Martin Heinrich Klaproth analyzed an ore, he determined the existence of a new metal oxide and called it ochra (ocha-colored soil). and the ore ochroite because it appears to be ochre when burning.
In the same year, the Swedish chemist Jöns Jakob Berzelius and the Swedish mineralogist Wilhelm Hisinger also analyzed the same new metal oxide, which is different from yttrium. Yttrium is dissolved in ammonium carbonate solution and appears red when burning on gas flame. However, this metal oxide is insoluble in ammonium carbonate solution and does not exhibit characteristic flame color when burning.
The ore is thus called ceria (bauxite), and the element is named cerium to commemorate the discovery of an asteroid, Ceres.
Three Early Applications of Cerium
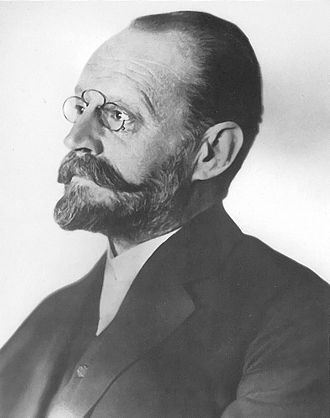
Eighty-three years after the discovery of “cerium”, in 1886, the Austrian Carl Auer von Welsbach found the first application of cerium (also rare earth) as a luminescent enhancer for steam hoods. He found that heating 99% thorium oxide and 1% cerium oxide would give off a strong light, so cerium used in coal gas lamp gauze can greatly increase the brightness of the gas lamp. The gas lamps in Europe, where electric lights were not yet popular, were the main source of lighting and were essential for industrial production, commerce, and life.
After the First World War, electric lights gradually replaced gas lamps, but cerium continued to open up new applications. In 1903, Welsbach once again discovered the second largest use of cerium. He found that cerium iron alloys can generate sparks under mechanical friction and therefore can be used to make flints. This classic use of cerium has been around for 100 years. Everyone who smokes knows that a lighter uses a flintstone, but many people they that it is cerium that brings fire to people.
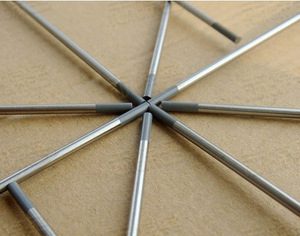
In 1910, the third important application of cerium was discovered for arc carbon rods in searchlights and film projectors. Similar to the steam cover, cerium can improve the efficiency of visible light conversion. Searchlights were once an important tool in war air defense. Arc carbon rods have also been an indispensable source of light for filming.
Modern Applications of Cerium
Since the 1930s, cerium oxide has been used as a glass decolorizer, clarifier, colorant, and abrasive polishing agent.
As a chemical decolorizer and clarifier, cerium oxide can replace the highly toxic white magnetic (oxidation) to reduce operational and environmental pollution.
The use of cerium titanium yellow pigment as a glass colorant produces a beautiful bright yellow art glass.
Cerium oxide as a main component to manufacture various specifications of polishing powder has completely replaced iron red polishing powder, greatly improving polishing efficiency and polishing quality.
As a glass additive, cerium can absorb ultraviolet light and infrared rays and thus has been widely used in automotive glass. It not only protects against UV rays but also reduces the temperature inside the car, thus saving air conditioning power.
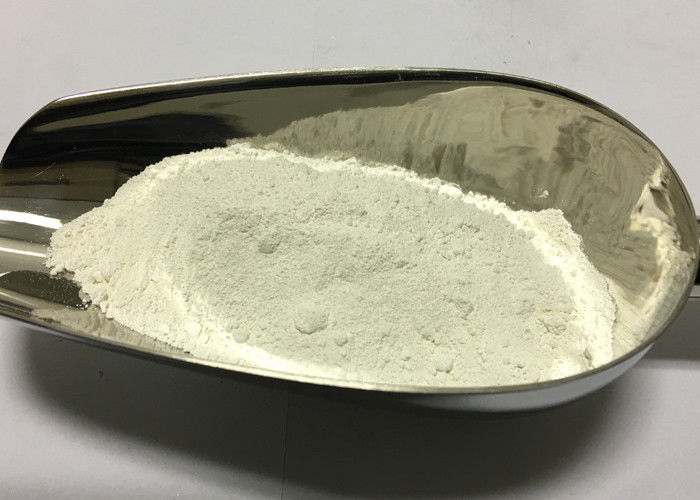
This history column aims at introducing the history of different metal elements. If you are a metal lover or history lover, you can follow our website. For previous posts of metal history, you can look them up in the “history” category.
Please visit https://www.sputtertargets.net/ for more information.